Featured Lendület Member: Imre Norbert Orbulov
Composite metal foams have played a significant role in many areas of industry over the last decades (for example, they are used in impact and blast protection of buildings and vehicles), but the methods used to develop them are now becoming less and less viable. Imre Norbert Orbulov, Dean of the Faculty of Mechanical Engineering at the Budapest University of Technology and Economics (BME), Professor of Materials Science and Technology, and head of the MTA-BME Research Group on High Performance Composite Metal Foams, and his colleagues are therefore exploring radically new approaches to the development of metal foams to help develop materials with significantly improved properties.
Orbulov has already been the leader of the Lendület research group, and in 2023 he won the grant in the H category (“Advanced”). The newly formed research group will continue the research of the previous tender, as it has been working on the development of composite metal foams in the Department of Materials Science and Technology of the Faculty of Mechanical Engineering at BME.
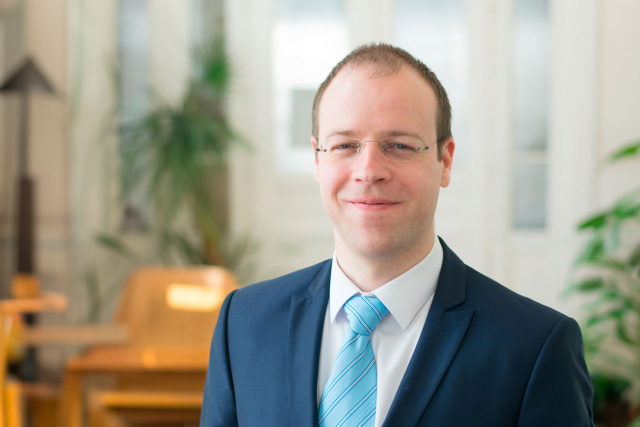
Metal foams are highly porous structures made of metal. Everybody encounters metal foams, even in their homes, as metal dishwashing sponges (for strong scrubbing) can be considered open-cell metal foams. Open-cell metal foams have interconnected cavities, while the other large group of metal foams, closed-cell metal foams, have bubbles separated by a wall.
Widely used ’young’ materials
A special subtype of closed-cell metal foams is syntactic or composite metal foams. They are composed of a metal matrix material and a porous filler. This filler may consist of hollow balls (the material itself is the shell – like a balloon or a ball), which are injected into molten metal, for example, to create the composite metal foam and thus lighten its structure. The density of the composite metal foam created in this way is reduced to approximately half the density of the original base metal. Although composite metal foams have been developed around the world for more than half a century, they are still considered to be a young material in materials science.
However, they are very widely used.
They are emerging as structural materials, especially where density reduction is important, such as in the automotive industry, where they can contribute to reducing the weight of a vehicle (e.g. an electric car).
“By now, the development of composite metal foams using classical methods has practically come to an end, as their specific mechanical properties (and other properties) can no longer be improved by established methods. Therefore, a completely new approach is needed to move forward,” says Orbulov. “Our research group is trying to find solutions to this problem.
In other words, one of our main goals is to improve the mechanical properties of composite metal foams using non-classical methods.
” This can be achieved by reinforcing the matrix material of the future composite metal foams (by particle or fibre reinforcement) or through the use of metal foams as load-bearing elements (e.g. sandwich panels or filled tubes).
Cost reduction, manufacturability, recycling
Cost reduction is an equally important objective of the research team. Metal foams using the commonly used ceramic spherical fillers are very expensive, but the research group leader argues that it is much cheaper to introduce porosity into metal foams, for example, with the use of clay pebbles. Clay pebbles are a fairly common and cheap material: they are used as mulch at the base of trees in parks.
If these clay pebbles, a few millimetres thick, are cut in half, a closed-cell can be found inside, which can be used to make composite metal foams.
But the Lendület researchers are also experimenting with changing the geometry of the filler material: they are elongating the spheres and trying to introduce porosity into the material with ellipsoidal shells. In another experiment, they will test the behaviour of spike-covered filler spheres.
“The manufacturability of large composite metal foams is severely limited. If engineers want to produce large structures from them, they have to be created in separate pieces, and then these pieces have to be fixed together,” continues Orbulov. “In the coming years, members of our Lendület research group will work to develop sealing joints with a material that creates a connection between the metal foams for this purpose . Welding and soldering are the best-known types of material-sealing joints, and we also plan to adapt these processes to composite metal foams. Finally, we will also investigate the recycling of composite metal foams.”
New findings turn into a university curriculum
Perhaps the most important property of composite metal foams from a practical application point of view is that they can absorb large amounts of energy when loaded.
This is why they were first used in automotive collision protection.
For example, this kind of metal foam fills the bumpers of Combino trams. Due to their force-absorbing capacity, metal foams can also play an important role in the defence industry. For example, they can be incorporated into the walls of protected buildings to increase the building’s resistance to explosions, and the same property can be useful in the armouring of combat vehicles.
“I would be satisfied at the end of the Lendület grant period if we could increase the mechanical energy absorption of composite metal foams by twenty to thirty percent,” said the leader of the research team. “I also hope that we can solve the problem of soldering metal foams (welding seems to be more problematic at the moment), and I would be satisfied if we could find a solution to recycling 60-70 percent of metal foams. In the meantime, we will incorporate our results and the procedures we have developed into technical university training.”