Featured Lendület Member: Andrea Toldy
How can waste from cross-linked polymers, which make up a smaller proportion of plastics, be recycled? Andrea Toldy, Professor in the Department of Polymer Engineering at the Budapest University of Technology and Economics, and head of the MTA-BME Lendület Sustainable Polymers Research Group, is seeking answers to this question with the support of MTA’s Lendület Programme.
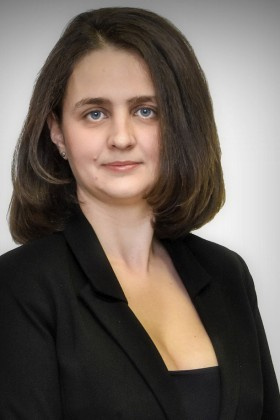
Andrea Toldy, a chemical engineer, has been working on cross-linked polymers since her student research projects. There are two main types of polymers: thermoplastic and cross-linked polymers. The former group can be melted above a certain temperature, making them easy to recycle. These polymers include many of the bulk plastics that are known from everyday usage.
Cross-linked polymers represent a smaller proportion of plastics in terms of volume, but are of great importance in relation to their mass because their properties allow them to be used in very specific applications – even where thermoplastic polymers cannot be used.
“Cross-linked polymers are typically engineering plastics with excellent mechanical properties, so durable products are usually produced from them,” said Toldy. “They are used to make wind turbine blades and aircraft parts, and other vehicle industry uses are also common. In other words, they are used to make structural parts that are subject to high stress.” Cross-linked polymers are fibre-reinforced to further increase strength, that is, the polymer is strengthened with a reinforcing material. In these plastics, the polymer effectively acts as the adhesive, while the fibre-reinforcing material is the load-bearing component. The latter component is typically a carbon fibre for high-tech applications. More than 60% of today’s aircraft are already made of such polymer composites, as they have the advantage of being much lighter than metals, in addition to having excellent mechanical properties. The lighter weight reduces aircraft fuel consumption, and in addition, they are also corrosion-resistant, making them more durable and safer for use in, for example, aircraft.
As their name suggests, these cross-linked systems have a three-dimensional chemical structure and, unlike thermoplastics, cannot be melted. In recent decades, the use of these cross-linked polymers has increased, and we have now reached a point where the management of the ever-increasing quantities of polymer waste is a growing concern. Aircraft made from these materials also have a finite lifespan and are scrapped after twenty to thirty years, and the large quantities of polymer waste generated need to be managed.
“There is a need for methods that can be used to recycle the waste from cross-linked polymers,” argues Toldy. “As these materials cannot be melted, there is currently only one recycling method that works on an industrial scale: pyrolysis. The principle of pyrolysis is that the polymer is broken down in an oxygen-free environment, and the resulting decomposition products are typically burned. In this way, the energy contained in them is harnessed, but the polymer itself is not recycled at the time, only the thermally stable fibre reinforcement left from the composite after pyrolysis.” However, at such high temperatures, even the carbon fibres are damaged and do not retain their original beneficial structure. To sum up:
the issue concerning the recycling of cross-linked polymers and their composites is far from being solved, and new polymer systems designed for recycling are needed, both from an industrial and environmental point of view.
It is precisely such processes and new materials that the Lendület research group aims to develop.
“In this project, we will be working on, among other things, a completely new family of materials called vitrimers, whose properties lie between thermoplastic and cross-linked systems,” said the research group leader. “The production of these materials was first published in 2011, and their structure is based on the chemical basis of dynamically-rearranged double bonds, a phenomenon that has been known for some time but had not been used in polymers before.”
The properties of vitrimers therefore form a bridge between thermoplastic polymers, which are easy to recycle, and cross-linked polymers, which have special mechanical properties. Vitrimers have the same 3D material structure as cross-linked polymers, but can be melted above a certain temperature. Moreover, they can even be endowed with self-healing properties, and these composites can be repaired by being heated. In other words, they combine the advantageous characteristics of groups of plastics that have hitherto been sharply separated.
According to Toldy, the development of vitrimers is currently at a very early stage, but could soon represent a breakthrough for the composites industry. For this reason, many research groups around the world are investigating them, as the successful solution of a number of problems depends on the use of vitrimers, for example, in the aerospace industry. One of the expectations is that vitrimer technology can be integrated into existing production lines, and that the glass transition temperature of vitrimers is suitable for the application. The glass transition temperature is the limit below which it is safe to use these polymer composites, as above this temperature their mechanical properties, such as strength and stiffness, are significantly reduced.
The research team is collaborating with a US company that is expected to be the first to produce vitrimers on an industrial scale in the near future.
Preliminary tests with the material have already begun. The team is trying to develop the technology for the production of polymer composites and methods for their recycling. Their aim is to recover the reinforcing material in its original fibrous structure, which can be achieved with certain solvents. They are currently investigating which kind of solvent should be used and under which parameters recycling should be carried out. If they succeed in recovering the original, high-quality carbon fibre reinforcement, they will then investigate its properties and the characteristics of the composites that can be recycled from it again. “We are also looking into the flame retardancy of vitrimer systems, which is very important because these composites can replace metals in the automotive and aerospace industries,” says Toldy. “On the other hand, the polymer matrix of composites is generally highly combustible, as most of them are petroleum derivatives, so they have very good combustion properties. So from a safety point of view, it is important to make them flame retardant. They should not ignite and, if they do, should have low heat and pollutant emissions. Flame retardancy can also be achieved with the use of various additives (called additive flame retardancy), but also by incorporating components such as phosphorus into the polymer system itself to make the material flame-retardant. This is the direction we will follow. The advantage of this approach is that no additives migrate to the surface of the polymer, and smaller amounts are sufficient for effective flame retardancy.”